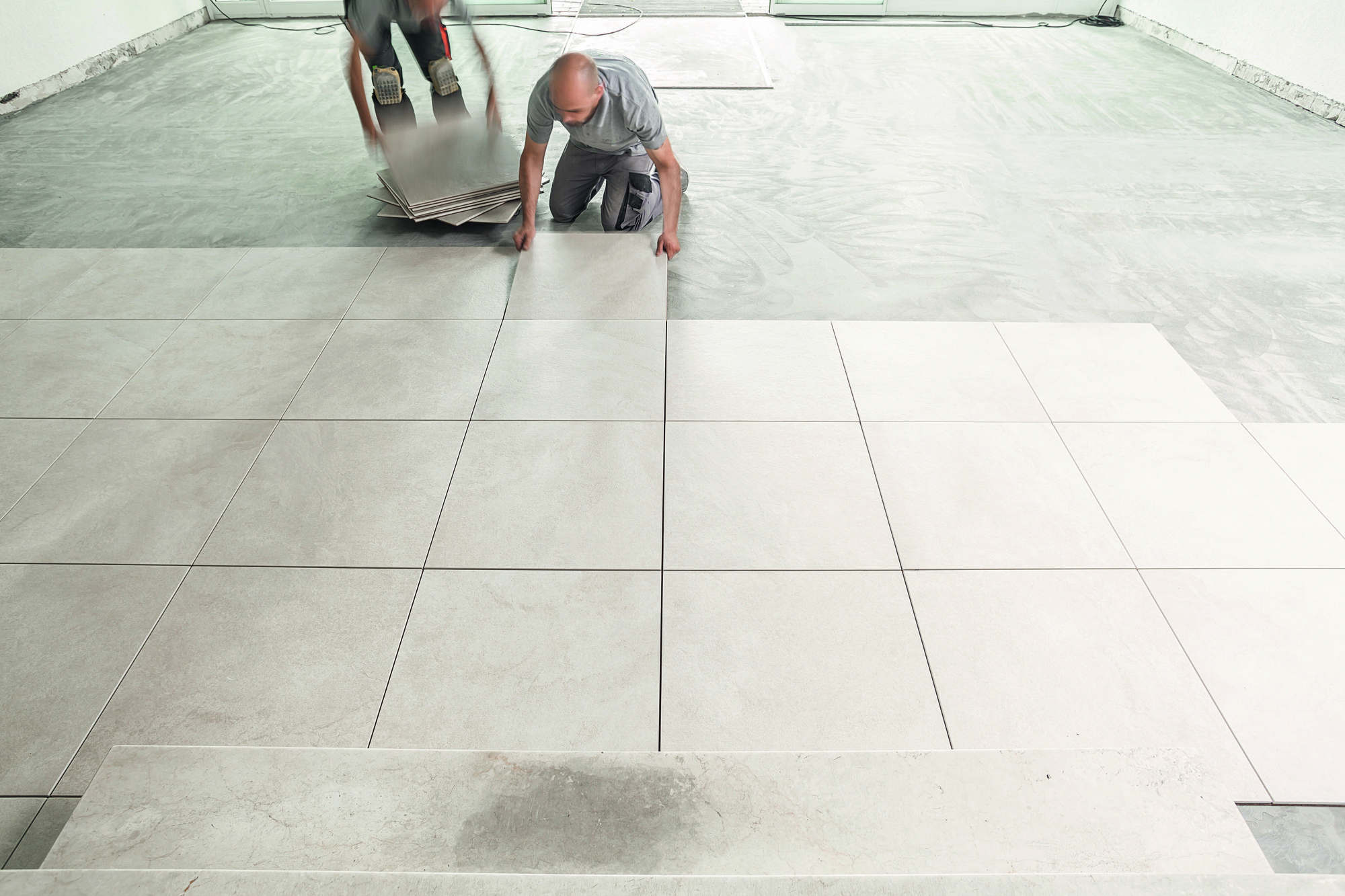
Ceramic Flooring That Can Be Installed 8 Times Faster Than Conventional Tiling
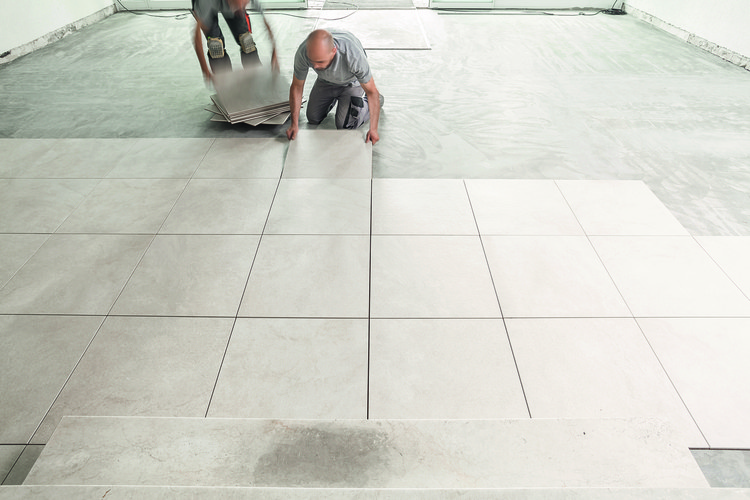
Flooring can either make or break a space. With the proper design, it can enhance a room’s design, mark a good first impression and positively impact user experience. However, because floors must withstand damaging conditions such as exposure to moisture and heat, constant foot traffic and heavy furniture movement, it is only natural for them to degrade over time. As a result, renovating floors is crucial to maintain interiors in a good state, especially those with a lot of use.
While selecting a new material to replace the old surface, building owners, architects and designers must consider many key factors, such as comfort, durability and aesthetics. But when it comes to buildings where daily functions are carried out and thus cannot be closed for long periods of time – like supermarkets, offices and restaurants –, speed of installation often becomes the top priority. Ultimately, as the old saying goes, “time is money.”
With this in mind, recent flooring innovations have focused on enabling a quick, easy and efficient installation, but without compromising visual appearance and resistance. For example, ceramic tile company AGROB BUCHTAL has developed DryTile, a new high-quality flooring system that can be installed with no adhesives and in record time – all while maintaining the look, beauty and properties of raw ceramic.
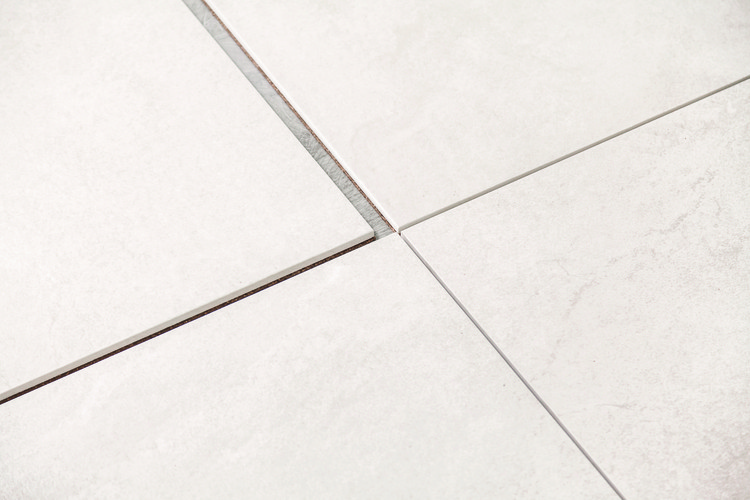
The components: ceramic, cork and system joint
Essentially, DryTile is a ceramic tile system, meaning it offers all the advantages that are characteristic of the material when compared to other floorings such as laminates or vinyl. Besides being UV, water and stain resistant, the tiles are odorless, non-flammable, light-fast, non-fade, recyclable, impervious to heat and free of any pressure marks from heavy furniture. But what’s unique about DryTile’s composition is that it includes a thin layer of cork under the tile that is specially developed. Free of PVC, chlorine and plasticizers, the layer is generated thermally under constant pressure and then applied permanently to the back of the ceramic. This ensures that the tile is firmly suctioned to the floor without the need of using a mortar bed and adhesives – a dry installation process, hence the product’s name.
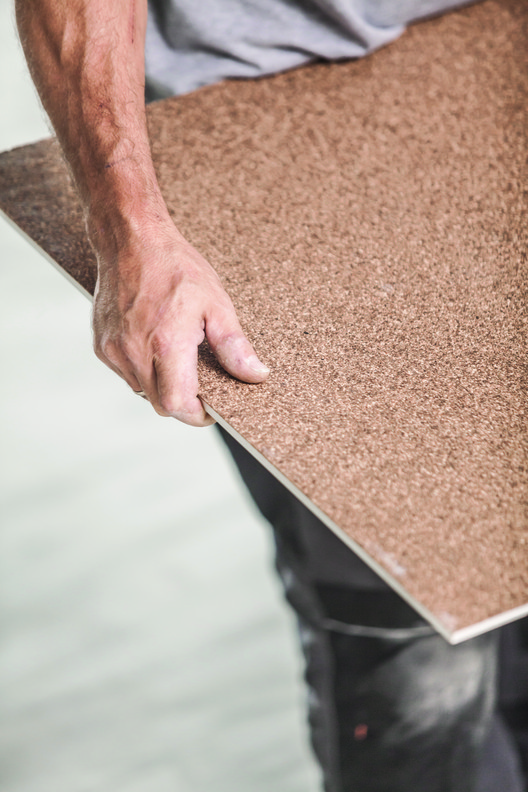
The principle is quite simple: with a vacuum-like effect, the tile’s inherent weight presses the cork layer onto the substrate where it adheres, guaranteeing that everything stays firmly in place. Enhanced by decoupling in the case of floating installation, the cork also improves impact sound installation. And by protecting the tile in transit, it also reduces packaging needs. Additionally, the cork layer has an exactly defined, slight projection on all four sides. Therefore, a system joint is automatically formed by laying the edges tightly against each other.

By combining the benefits of ceramic and cork, the result is an innovative, large-format porcelain stoneware system that can be laid loose as floating construction on new or existing subfloors.
Quick, easy and efficient installation
So, how does the dry tiling installation actually work? Simply put, it all comes down to three simple steps. The only prerequisite for laying this type of flooring is having a sufficiently smooth subsurface, which implies that it must be examined for evenness and surface quality prior to installation. Thus, the first step is checking planarity by using the necessary measuring instruments. Sometimes, in order to ensure that this requirement is met, the floor must be reworked accordingly. Then, the joint grid is specified and the cork edges are laid tightly against each other. Finally, the last step is to grout the tiles using special dispersion joint mortar, which must consider the correct mixing ratio with water according to the manufacturer’s instructions.
Before pointing, the surface can be walked on immediately, allowing the continuation of other tasks like painting, drywall work or electrical installation. After pointing, it can be walked on after 12 hours and is fully resistant after another 12. It is also practically dust-free, decreasing dust exposure for construction workers. And if certain areas are subject to a change of use, breakage or suffer from any other kind of damage, the tiles can be removed entirely reversibly and immediately replaced without much mess and dirt – joints are easily cut open, drying times are avoided and the new tile is simply regrouted. At the same time, by simply being removed and reused, DryTile is taking a step towards a circular economy.
Minimizing impact on businesses by reducing closing times
Altogether, DryTile saves construction time, offers flexibility and enables an optimized installation. Compared to traditional tiling, the process is up to 8 times faster, making it ideal for buildings that must minimize their closing times. For example, it is suitable for supermarkets, where renewing a floor usually requires great technical efforts and consumes time that affects the business. This has already been successfully tested: in a food product market in Much, Germany, 2,000 sqm of DryTile flooring was laid in only four working days, a fraction of the time that is required for conventional re-flooring.
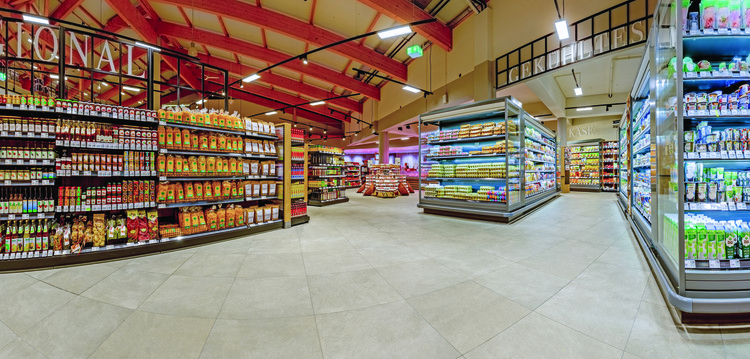
Apart from supermarkets, the product’s versatility and durability means it can also be applied in many other projects. In a range of natural tones – from cream to clay-brown and graphite – it can be used in all kinds of commercial interiors, showrooms, offices, museums, stores, schools and restaurants, among others.
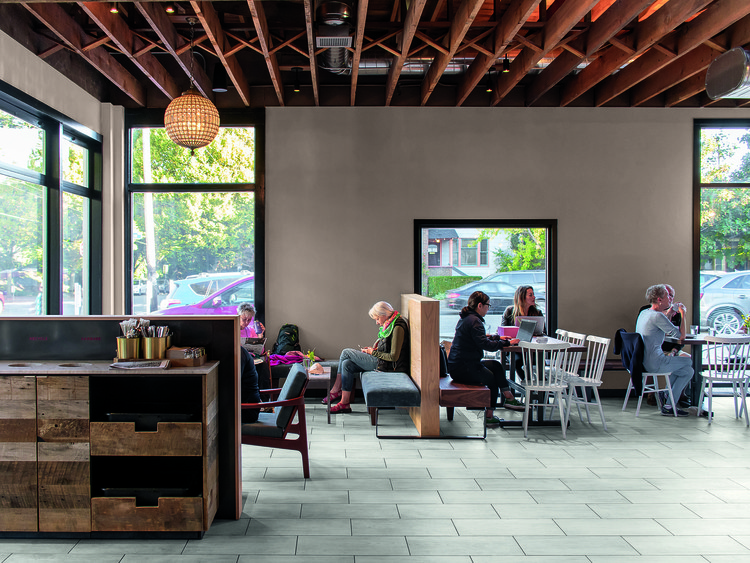

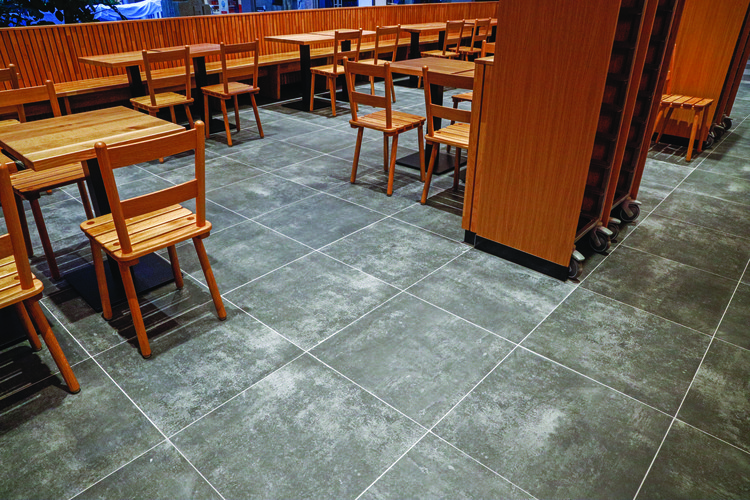
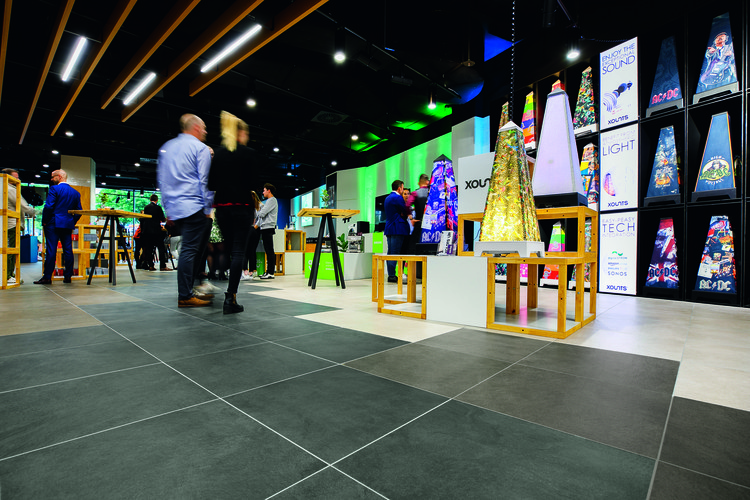
In a fast-moving world where new design trends point towards increased flexibility, flooring innovations like these show great promise by allowing surfaces to quickly adapt to new necessities, providing a timeless and versatile aesthetic, improving working conditions and optimizing the entire construction process.
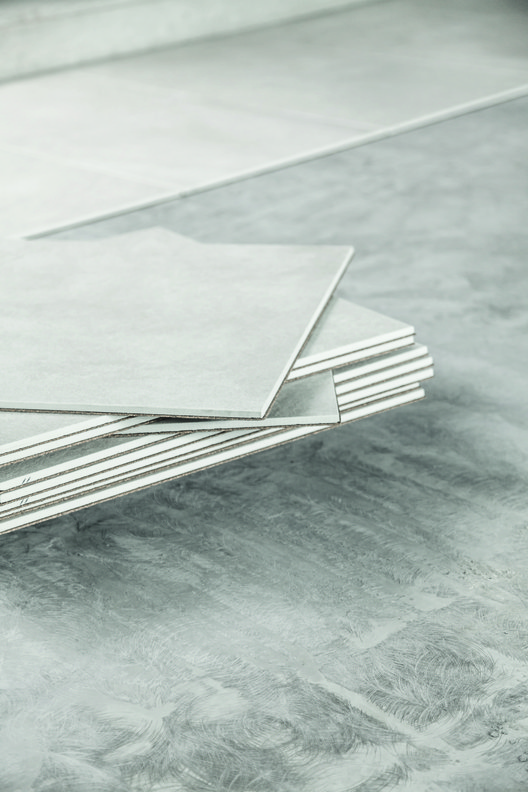
To learn more, visit DryTile’s website or social media channels (Facebook and Instagram).